PlanDoCheckAct
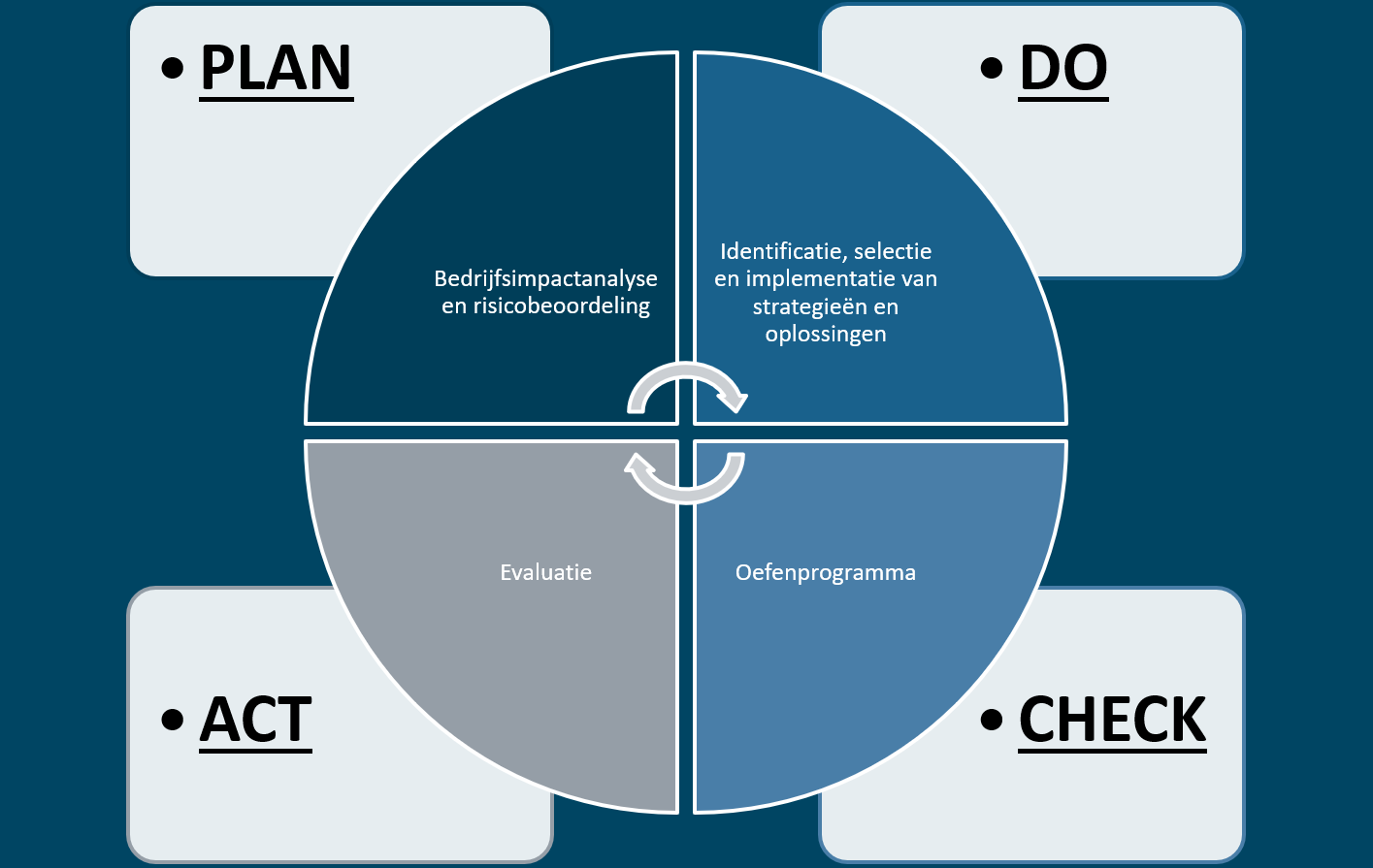
Plan Do Check Act Uitleg Passe IMAGESEE
The plan do check act cycle is not limited to big businesses or specific industries; it can be used by anyone who wants to continuously improve processes. Healthcare. In hospitals, patient care is the most important. By using the PDCA cycle, hospitals can make patient admissions easier, improve treatment plans, and perform better after-care.
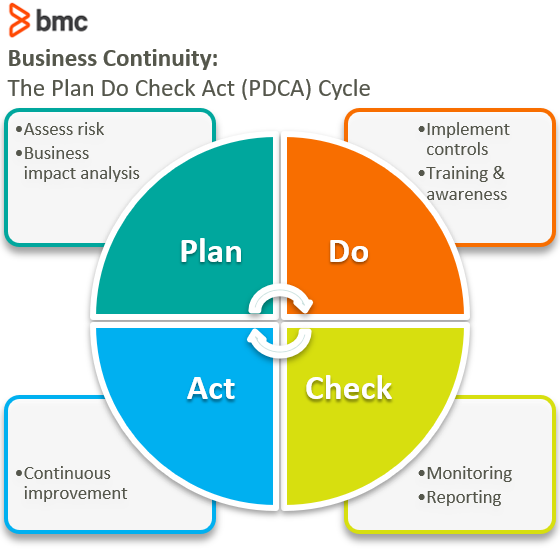
plandocheckactcycle BMC Software Blogs
Plan-do-check-act, or PDCA, is a method organizations use to continually improve their internal processes, increasing the quality of their products and the overall efficiency of their business.
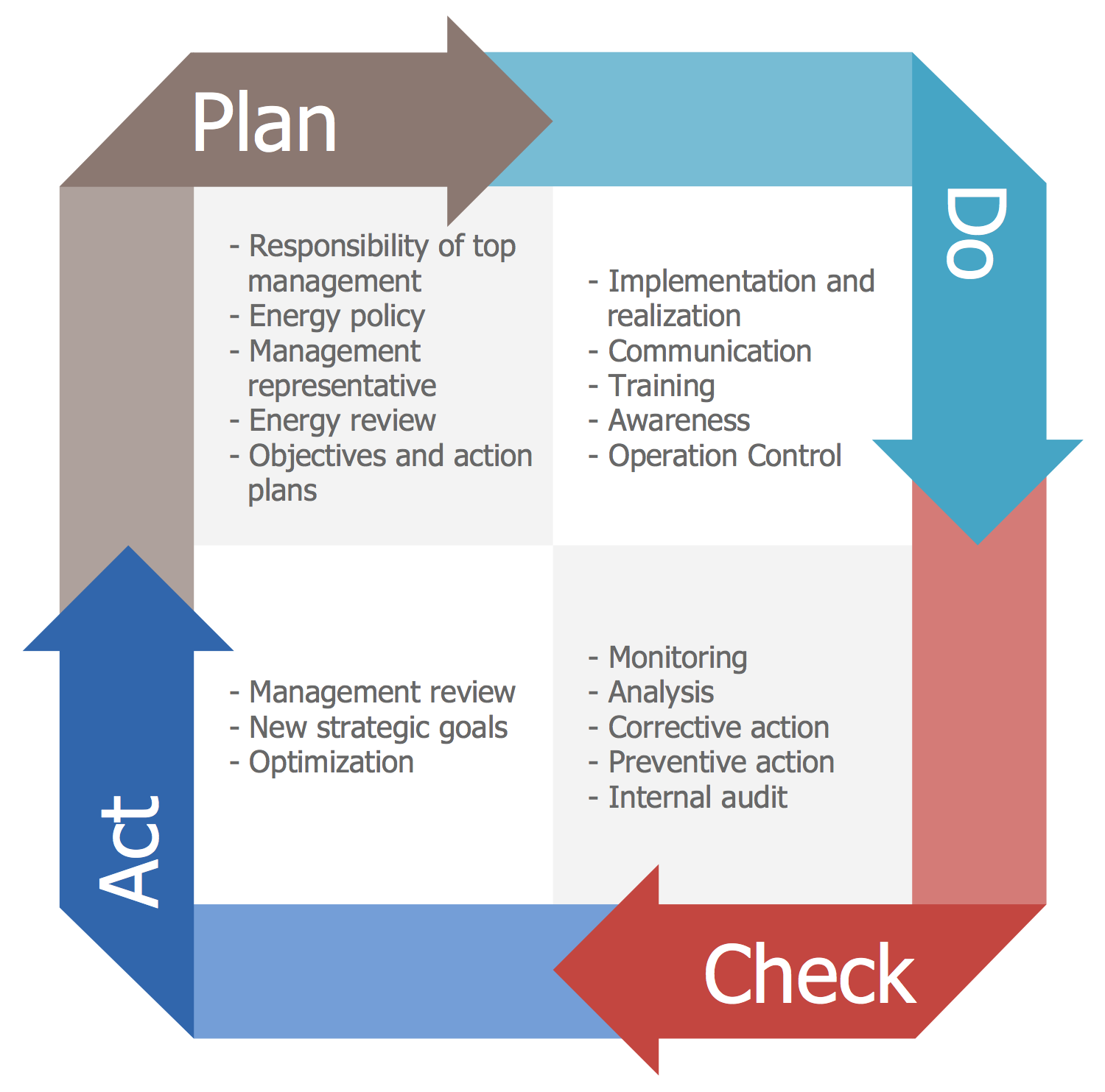
Plan Do Study Act Template
The Plan-Do-Check-Act (PDCA) cycle is a quality management methodology that aims to continuously improve processes.. This continual improvement approach was first developed and used in the 1950s by Dr. William Edwards Deming and since then it gained popularity and is now used by many organizations. Originally, the concept used by Deming was Plan-Do-Study-Act (PDSA), a systematic method used to.

How to use a proven method to fix your problems Business West
Plan-Do-Check-Act Cycle (PDCA) is a four-step, iterative by-design method used for control and continual improvement of processes and products. It is also known as the Plan-Do-Study-Act (PDSA) cycle, Deming cycle, Control Circle/Cycle or the Shewhart cycle. The PDCA cycle (Image source: Shutterstock [1]) PDCA is an evidence-based participatory.

Plan Do Check Act de PDCAcyclus tilt je bedrijf naar het volgende niveau De Zaak
PDCA (Plan-Do-Check-Act) is an iterative, four-stage approach for continually improving processes, products or services, and for resolving problems. It involves systematically testing possible solutions, assessing the results, and implementing the ones that have shown to work. It is based on the scientific method of problem-solving and was.
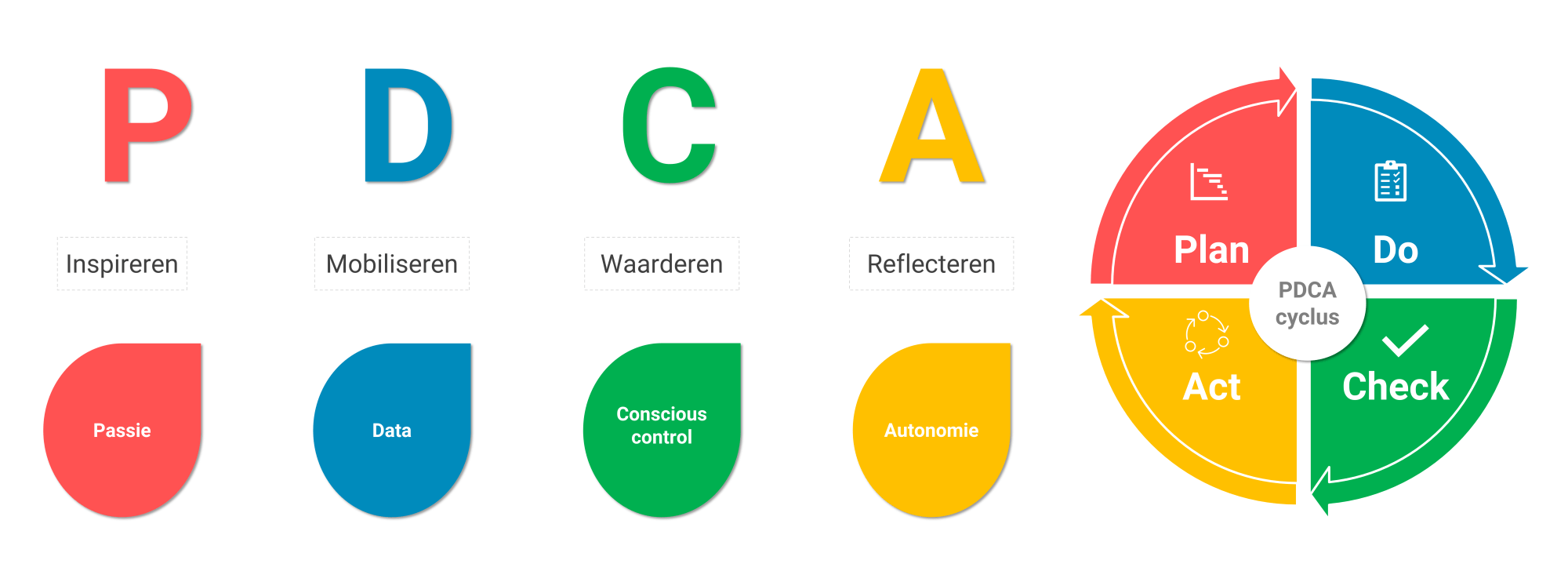
PDCA cyclus Plan Do Check Act uitleg 2 Deming cirkels
Act. Plan-Do-Check-Act (PDCA) provides a simple but effective approach to problem solving, managing change, ensuring ideas are appropriately tested before committing to full implementation in the "act" phase. Benefits include: Simple standardized method of improvement. Repeatable and consistent. Serves as an over-arching model for all other.
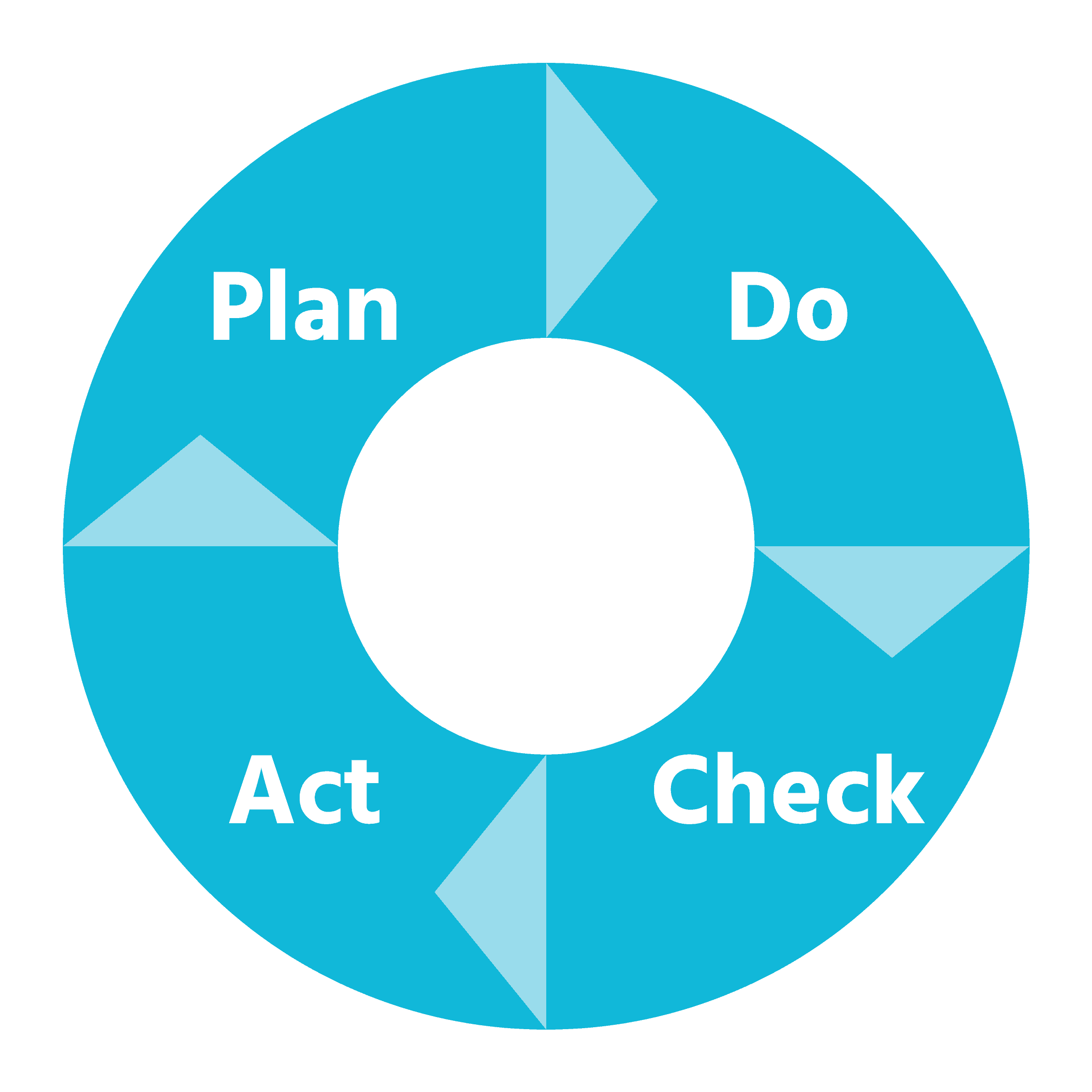
Pdca Cyclus 4 Stappen Plan Do Check Act Voorbeelden Images
PDCA is een afkorting die staat voor de 4 stappen van de PDCA cyclus Plan Do Check en Act. Je kunt deze stappen als hulpmiddel inzetten om processen te verbeteren en de kwaliteit ervan te verhogen. Met de toevoeging van het woord "cyclus" wordt bedoeld dat het werk nooit af is. Na het doorlopen van de Act fase, maak je nieuwe plannen om het.
.jpg?width=1548&name=PDCA (2).jpg)
PlanDoCheckAct
The Plan-Do-Check-Act model is a particularly useful tool for companies who follow the Kaizen method. Kaizen is an organizational mindset and culture focused on small, frequent changes that lead to significant improvements over time.

Plan Do Check Act Understanding And Applying Pdca Plutora Winder Folks
The Plan-do-check-act Procedure. Plan: Recognize an opportunity and plan a change. Do: Test the change. Carry out a small-scale study. Check: Review the test, analyze the results, and identify what you've learned. Act: Take action based on what you learned in the study step. If the change did not work, go through the cycle again with a.

Description of Check Act Plan Do Model Business901
The PDCA Cycle is a four-stage iterative framework aimed at continuous improvement. It involves planning (Plan), executing (Do), assessing and analyzing results (Check), and making necessary adjustments and enhancements (Act). This cycle helps organizations improve processes, products, and services over time. Origin.

Deming’s PlanDoCheckAct Cycle LaConte Consulting
The PDCA cycle has four stages: Plan — determine goals for a process and needed changes to achieve them. Do — implement the changes. Check — evaluate the results in terms of performance. Act — standardize and stabilize the change or begin the cycle again, depending on the results. PDCA is the foundation of continuous improvement or kaizen.
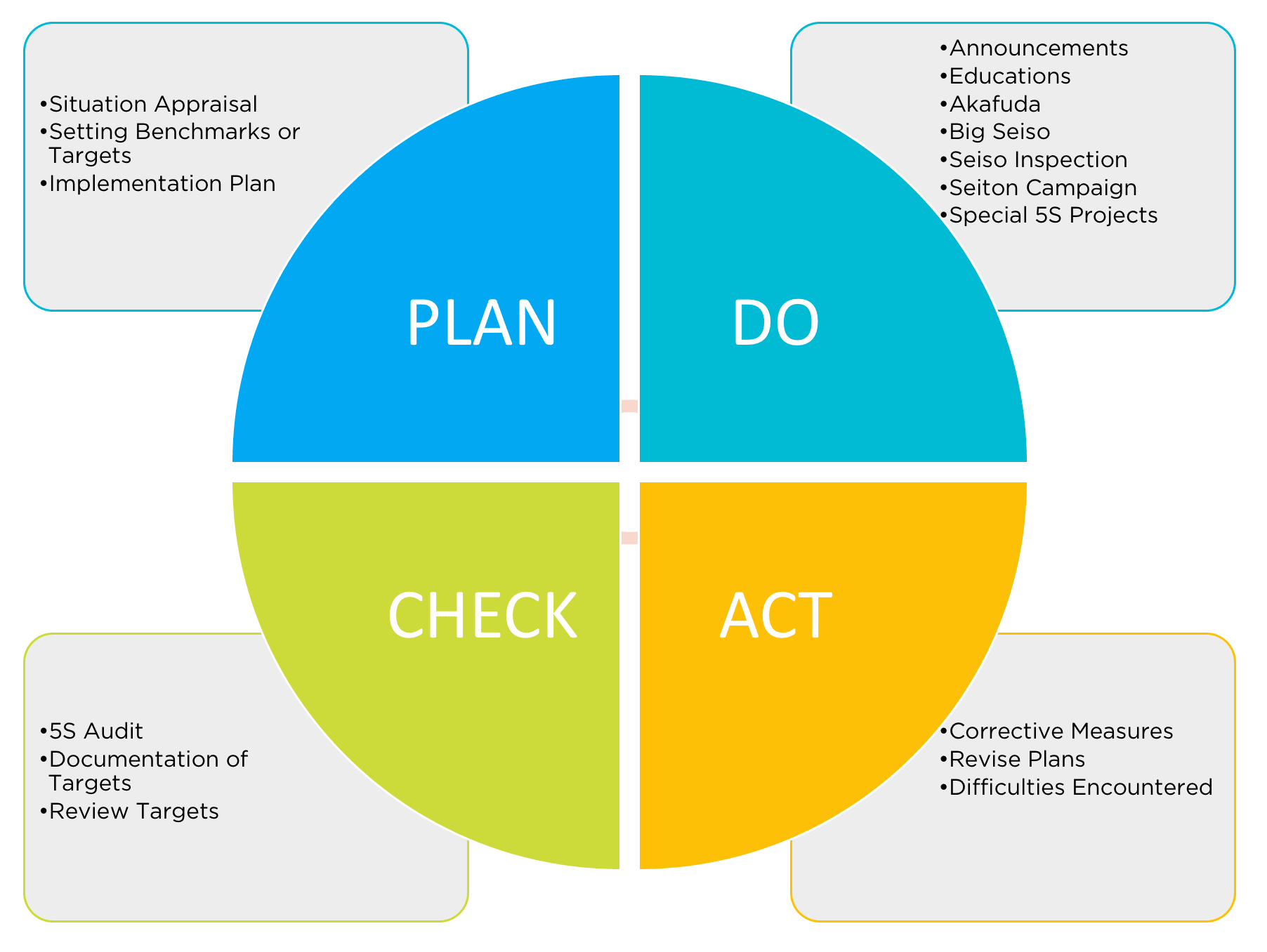
Plan Do Check Act Template Excel
The Plan, Do, Check, Act (PDCA) framework is a robust methodology for continuous improvement that has gained widespread popularity in both business and non-business contexts. In essence, it is a structured problem-solving approach involving the eponymous phases: Plan, Do, Check and Act. The framework is used by organisations of all sizes and.
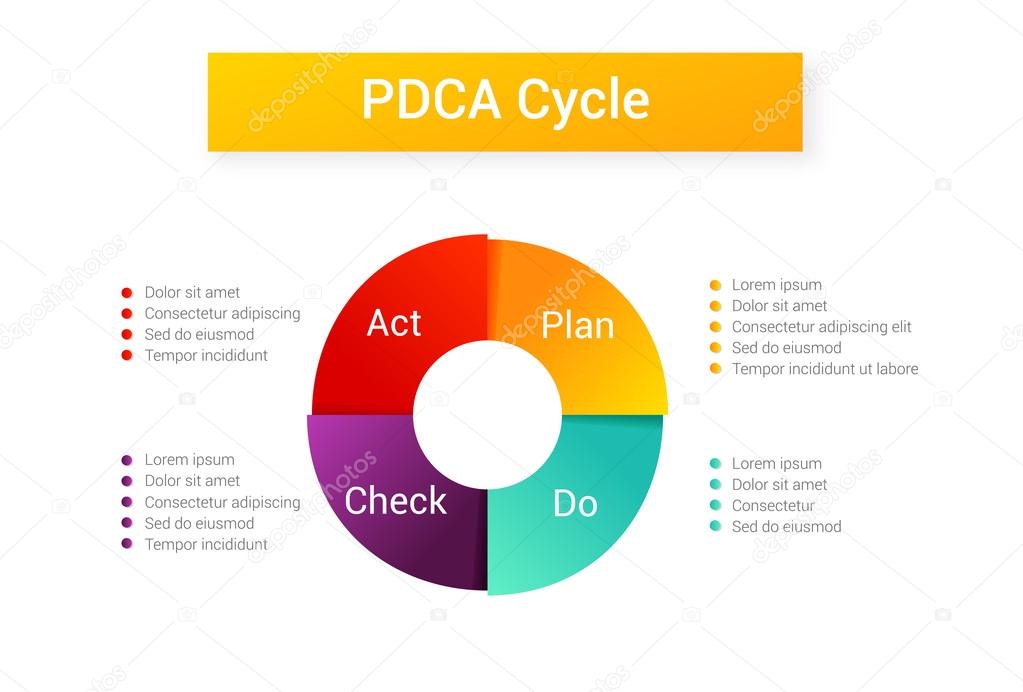
Plan Do Check Act Illustration Pdca Cycle Diagram Management Method Images and Photos finder
April 19, 2016 by Christoph Roser. Plan-Do-Check-Act (or PDCA) is one of the key elements in lean manufacturing, or for that matter in any kind of improvement process. In my view, it is the most basic framework for any kind of change. All other lean tools are only on top of the PDCA. In my experience, most lean projects in the Western world.
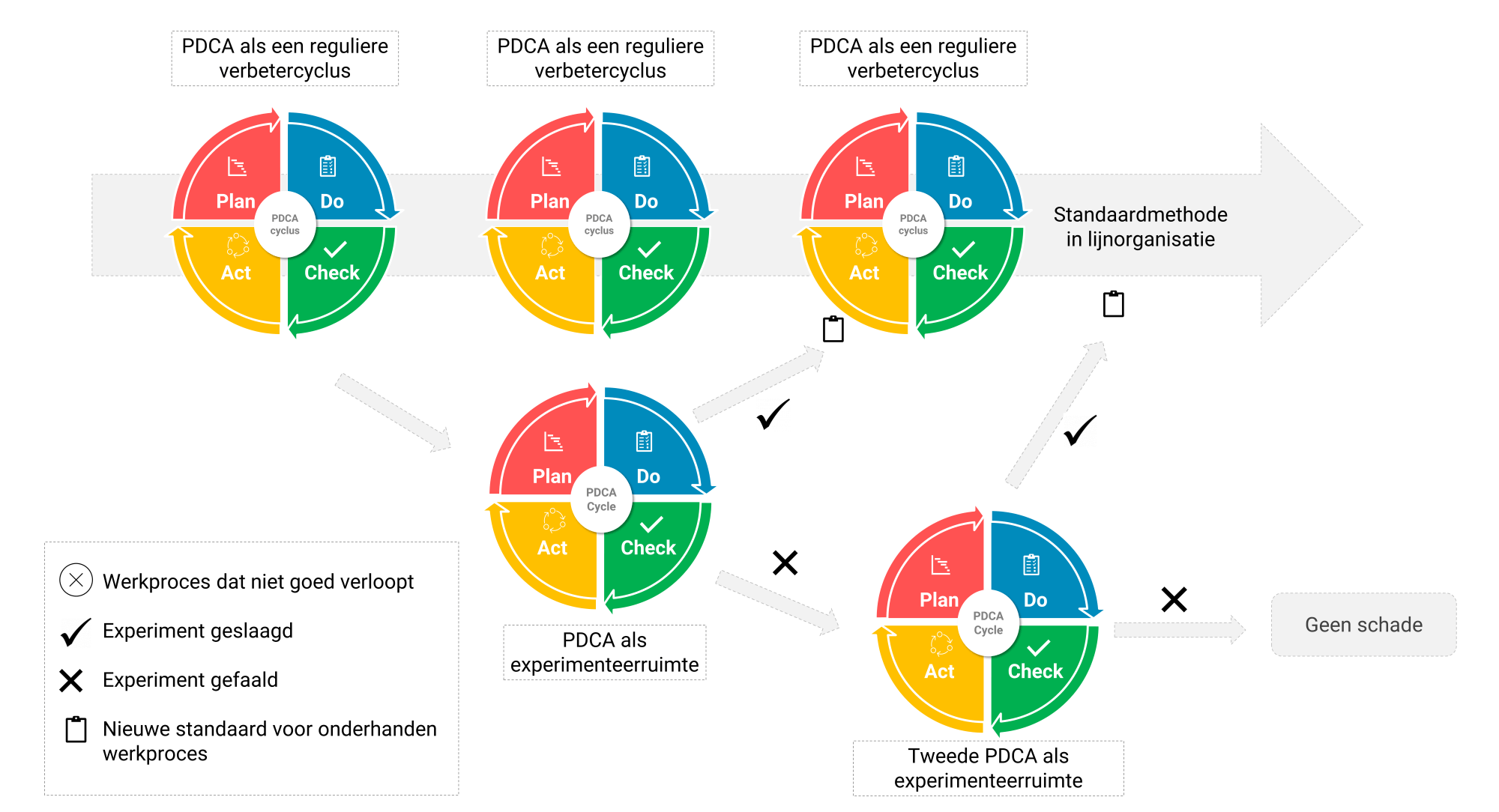
PDCA cyclus Plan Do Check Act uitleg 2 Deming cirkels
PDCA is a framework that turns a project into a continuous loop of planning, doing (setting the plan into action), checking (or evaluating the results) and acting (standardizing the plan or making adjustments). Each cycle builds on the lessons from the last one until your project is done. It makes projects more manageable and reduces the.
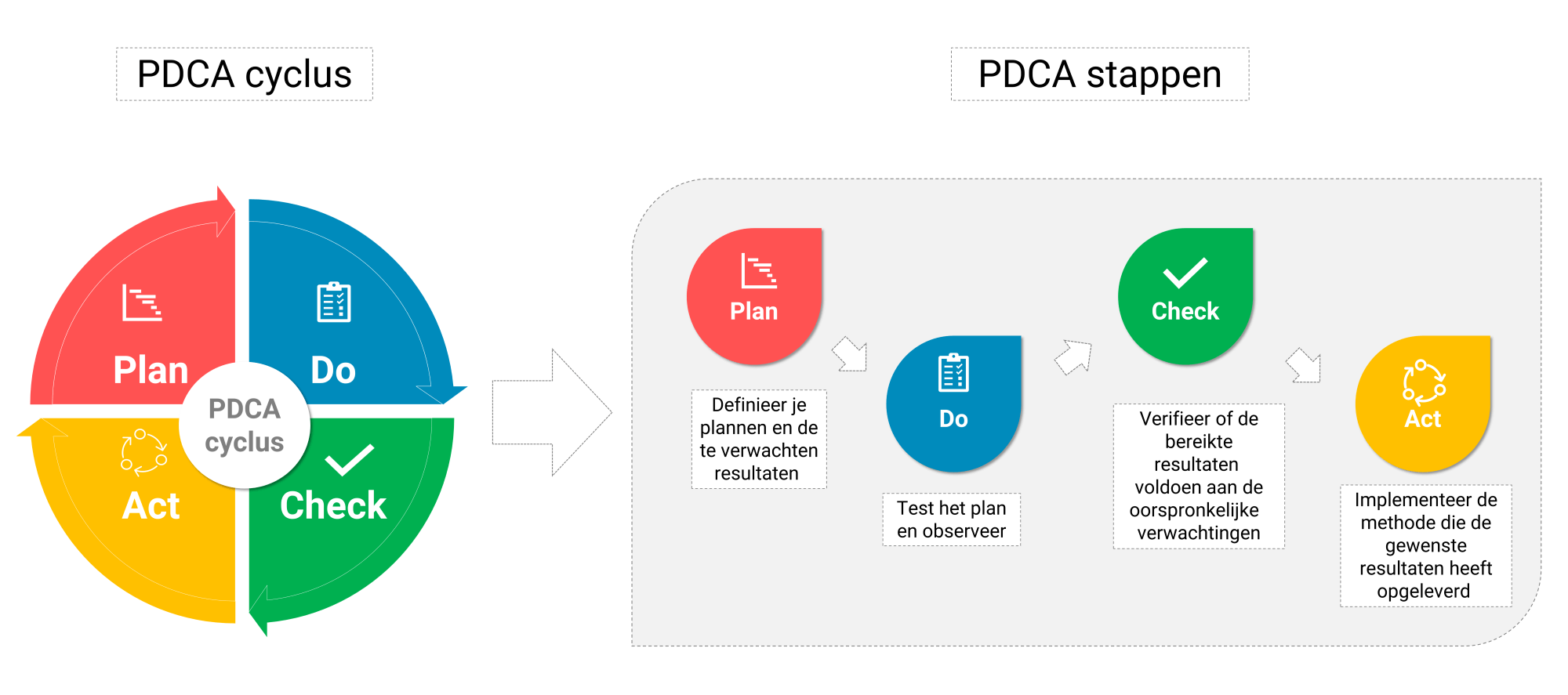
PDCA cyclus Plan Do Check Act uitleg 2 Deming cirkels
PDCA or plan-do-check-act (sometimes called plan-do-check-adjust) is an iterative design and management method used in business for the control and continual improvement of processes and products. It is also known as the Shewhart cycle, or the control circle/cycle.Another version of this PDCA cycle is OPDCA. The added "O" stands for observation or as some versions say: "Observe the.
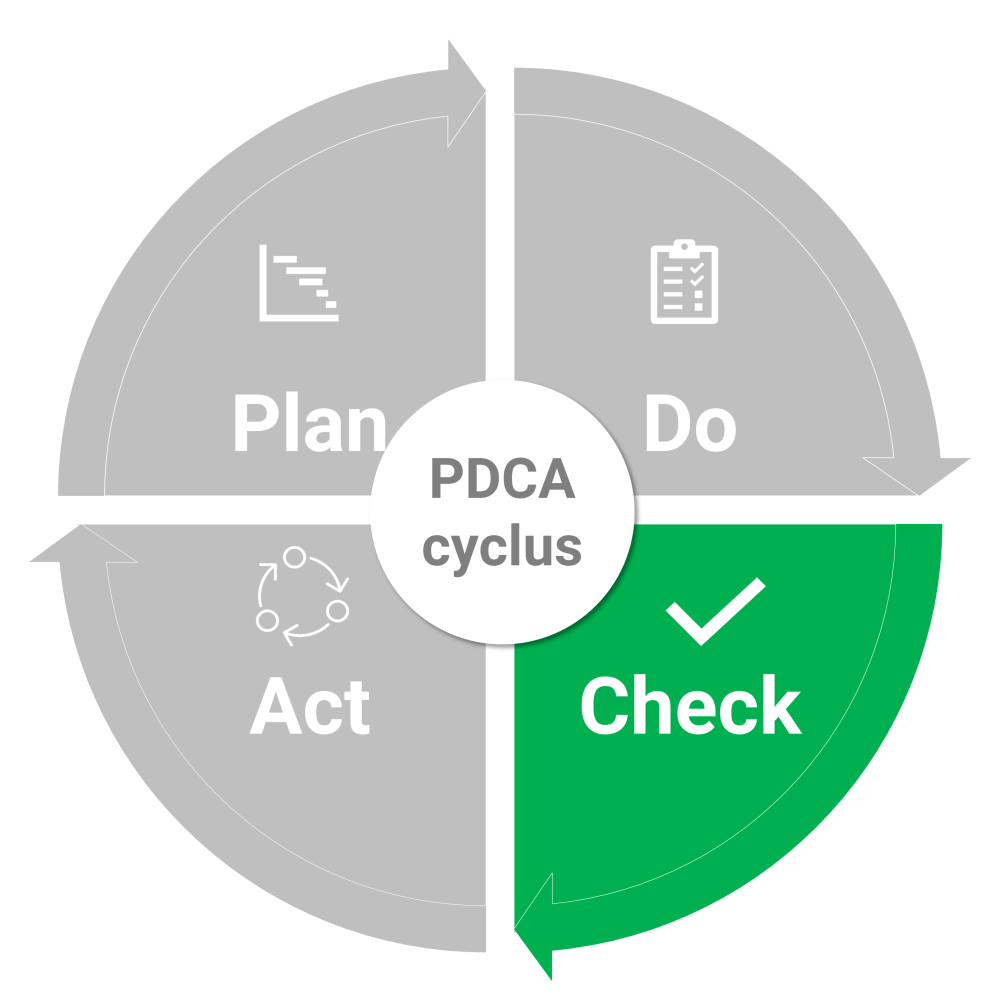
PDCA cyclus Plan Do Check Act uitleg 2 Deming cirkels
PDCA Cycle: A four-step problem-solving iterative technique used to improve business processes. The four steps are plan-do-check-act. The PDCA Cycle can be used to effect both major performance.